In the field of manufacturing, there is a process known as subtractive manufacturing that is quite intriguing. Unlike additive manufacturing, which adds material layer by layer, subtractive manufacturing involves removing material from a solid block to achieve the desired shape. This method has been in existence for centuries in different forms, evolving alongside technological advancements to become a fundamental part of modern manufacturing processes. In this article, we will explore the details of subtractive manufacturing, its applications in various industries, and its impact on the future of production.
Historical Evolution:
The roots of subtractive manufacturing can be traced back to ancient civilizations where craftsmen used primitive tools like chisels and hammers to carve and shape materials such as stone, wood, and metal. As civilizations progressed, so did the techniques and tools used for subtractive processes. The Industrial Revolution marked a significant turning point with the advent of machine tools like lathes, milling machines, and grinders, enabling more precise and efficient material removal.
Types of Subtractive Manufacturing Processes:
1.Milling:
Milling machines use rotary cutters to remove material from a workpiece, creating complex shapes and designs. The workpiece is secured on a platform, and the cutter moves along multiple axes to achieve the desired dimensions. CNC (Computer Numerical Control) milling has revolutionized this process, allowing for automated, high-precision machining.
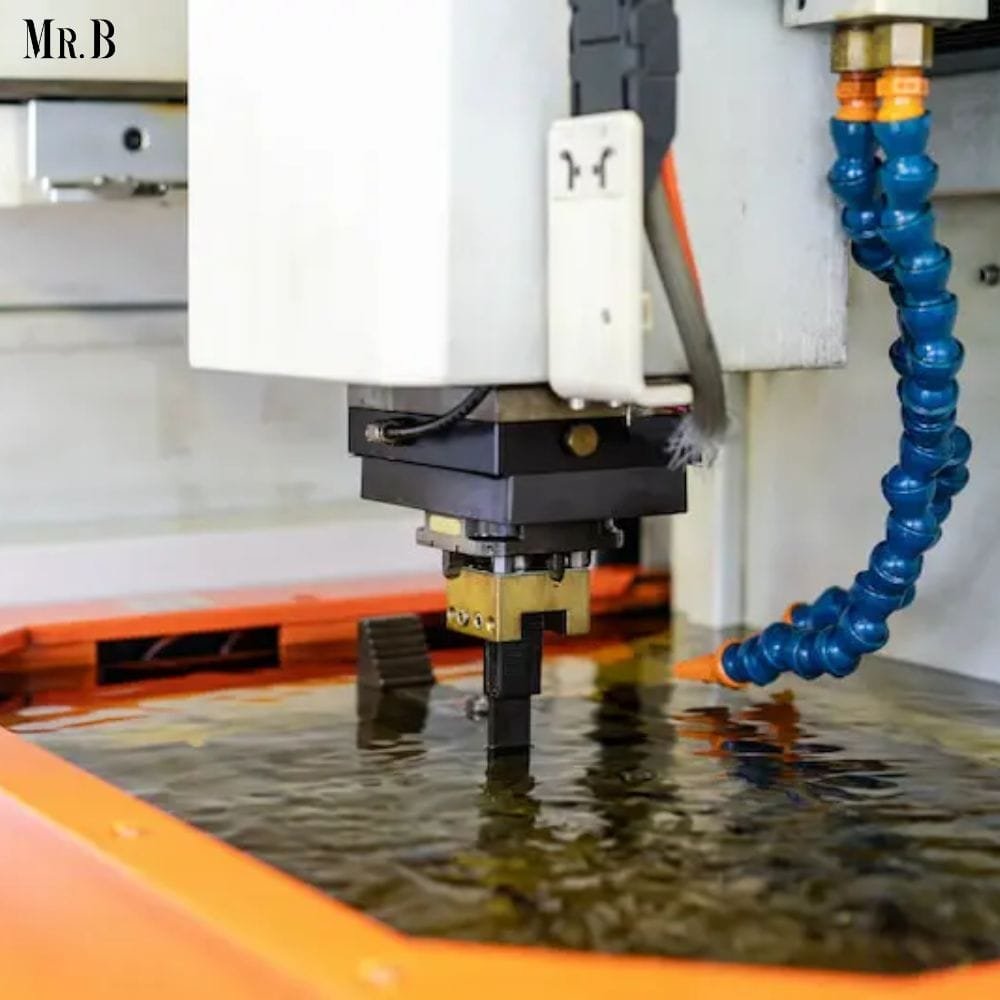
2.Turning:
Turning is primarily used for cylindrical or round-shaped objects. A lathe machine holds and rotates the workpiece while a cutting tool removes material symmetrically, resulting in shapes like shafts, gears, and threads.
3.Drilling:
Drilling involves creating holes in a workpiece using specialized drill bits. This process is crucial in various industries such as aerospace, automotive, and construction for assembly and component integration.
4.Grinding:
Grinding utilizes abrasive wheels to remove material and achieve precise surface finishes. It is commonly used for finishing operations to ensure tight tolerances and smooth surfaces.
5.EDM (Electrical Discharge Machining):
EDM is a non-traditional subtractive process where electrical discharges between an electrode and the workpiece erode material, particularly in hard-to-machine materials like hardened steel and titanium.
Applications Across Industries:
1.Automotive:
Subtractive manufacturing plays a vital role in automotive production, from machining engine components to creating intricate molds for body panels. High-precision milling and turning operations ensure the reliability and performance of critical parts.
2.Aerospace:
In aerospace manufacturing, where safety and precision are paramount, subtractive processes are used extensively for crafting turbine blades, aircraft structures, and complex components requiring tight tolerances and lightweight designs.
3.Medical:
Medical device manufacturing relies on subtractive processes for producing implants, surgical instruments, and prosthetics with biocompatible materials like titanium and stainless steel. CNC machining ensures precise dimensions crucial for medical applications.
4.Consumer Electronics:
The sleek and intricate designs of modern gadgets like smartphones and laptops are made possible through subtractive manufacturing. CNC machining creates precise casings, connectors, and internal components with minimal material wastage.
5.Tooling and Mould Making:
Subtractive manufacturing is integral to creating molds and dies for injection molding, casting, and forming processes across industries. CNC machining ensures the replication of intricate designs with high repeatability.
Advantages of Subtractive Manufacturing:
1.Precision:
Subtractive processes offer high precision and accuracy, crucial for industries such as aerospace, automotive, and medical where tight tolerances are required for safety and performance.
2.Material Versatility:
Subtractive manufacturing can work with a wide range of materials, including metals, plastics, ceramics, and composites, providing flexibility in production.
3.Surface Finish:
Many subtractive processes, such as grinding and finishing operations, can achieve smooth surface finishes and tight surface tolerances, eliminating the need for additional polishing or post-processing.
4.Scalability:
Subtractive manufacturing is scalable from small-scale prototyping to large-scale production, making it suitable for various production volumes and requirements.
Challenges and Future Trends:
1. Material Wastage:
Traditional subtractive processes can result in significant material wastage, especially for complex designs where excess material needs to be removed.
2.Energy Consumption:
Subtractive manufacturing processes can be energy-intensive, especially for high-speed machining operations and large-scale production runs.
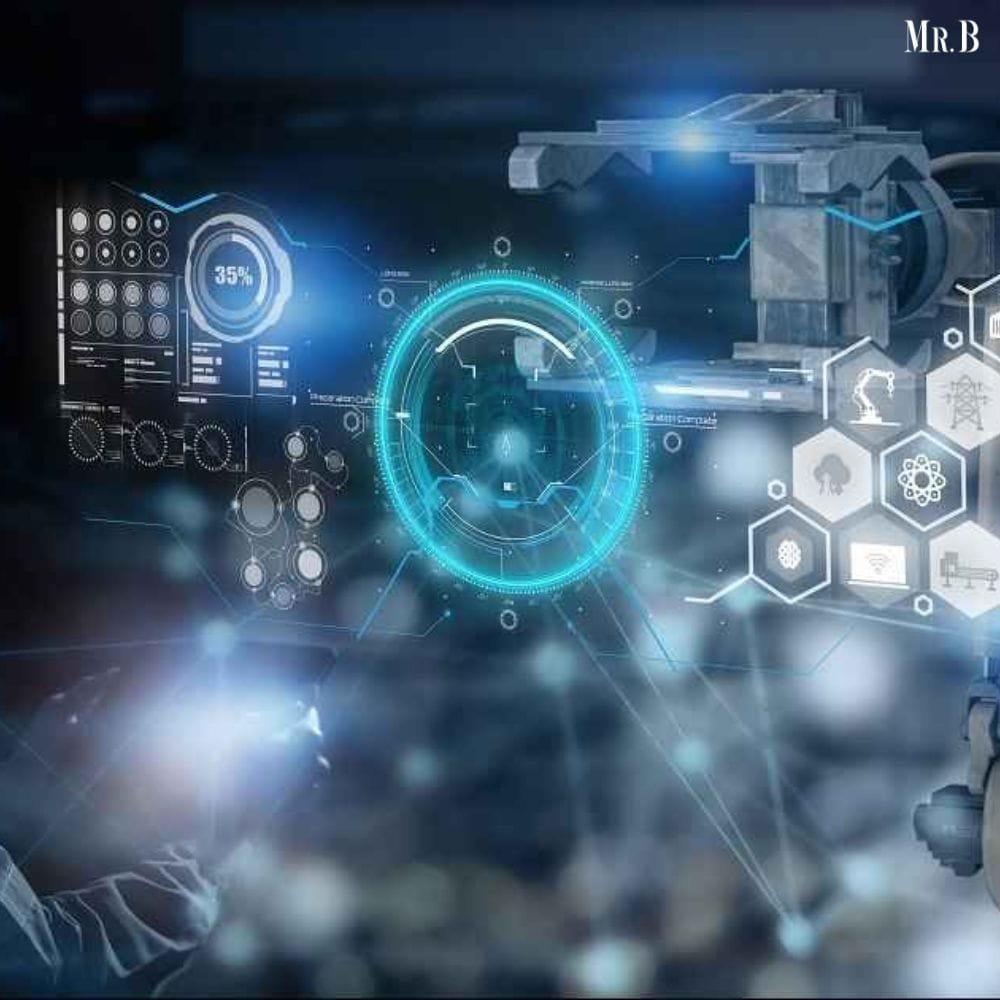
3.Automation and Industry 4.0 Integration:
The future of subtractive manufacturing lies in automation and integration with Industry 4.0 technologies such as AI, IoT, and data analytics. Smart machining centers and CNC systems will optimize production processes, reduce downtime, and enhance quality control.
4.Additive-Subtractive Hybrid Approaches:
Combining additive and subtractive processes offers the benefits of both worlds—complex geometries and material savings from additive methods, coupled with high precision and surface finish from subtractive processes.
5.Sustainability Initiatives:
Sustainable manufacturing practices are becoming increasingly important in today’s global landscape. Subtractive manufacturing can contribute to sustainability through optimization of material usage, recycling of scrap materials, and implementing eco-friendly machining techniques such as dry machining and minimum quantity lubrication (MQL). These efforts reduce waste generation, energy consumption, and environmental impact, aligning with the goals of green manufacturing.
6.Advanced Materials and Technologies:
The evolution of materials, including advanced alloys, composites, and ceramics, poses both challenges and opportunities for subtractive manufacturing. New cutting tools, coatings, and machining strategies are being developed to effectively machine these materials, ensuring high-quality parts with extended tool life and reduced machining times.
7.Digital Twin and Simulation:
The concept of digital twins, virtual replicas of physical assets, is revolutionizing manufacturing processes, including subtractive manufacturing. By creating digital twins of machine tools, workpieces, and processes, manufacturers can simulate and optimize machining operations, predict tool wear, and improve overall productivity and efficiency.
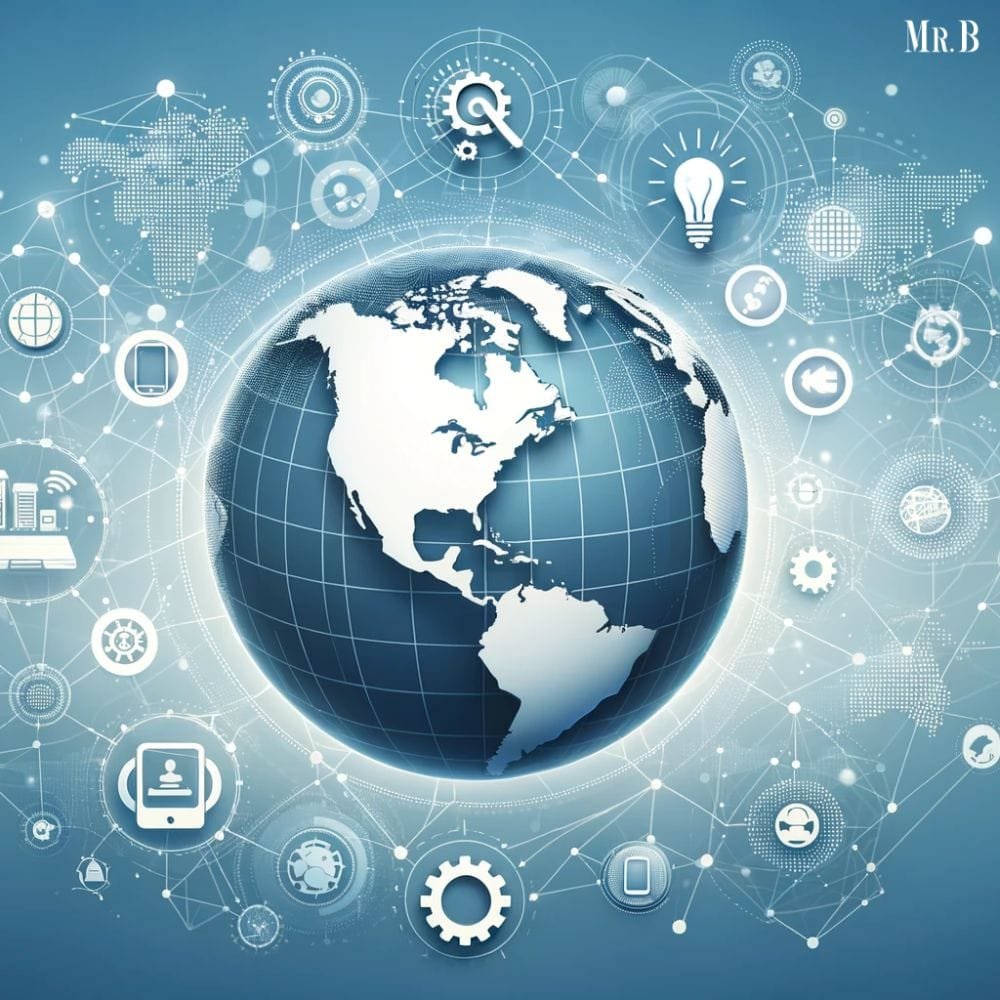
8.Global Supply Chain Resilience:
Recent disruptions in global supply chains due to geopolitical factors, natural disasters, and pandemics have highlighted the importance of resilience and agility in manufacturing. Subtractive manufacturing, especially when integrated with digital technologies like cloud-based CAD/CAM systems and real-time monitoring, can enhance supply chain visibility, reduce lead times, and enable rapid response to changing market demands.
9.Skill Development and Training:
As subtractive manufacturing technologies become more advanced and automated, there is a growing need for skilled operators, programmers, and maintenance personnel. Training programs focusing on CNC machining, CAD/CAM software, robotics, and digital manufacturing will play a crucial role in developing a competent workforce capable of leveraging the full potential of subtractive processes.
10.Customization and Personalization:
The ability to create highly customized and personalized products is a significant advantage of subtractive manufacturing. From custom orthopedic implants to bespoke automotive components, CNC machining and other subtractive techniques allow for intricate designs and individualized solutions tailored to specific customer needs, preferences, and requirements.
Conclusion:
Subtractive manufacturing continues to be a cornerstone of modern industrial production, offering precision, versatility, and scalability across diverse industries. As we move towards a more digital, sustainable, and interconnected manufacturing ecosystem, integrating advanced technologies, sustainability practices, and talent development will drive innovation and competitiveness in subtractive manufacturing processes. By embracing the opportunities and addressing the challenges, manufacturers can unlock new possibilities and deliver value-added solutions to meet the evolving demands of global markets.
Curious to learn more? Explore our Article on: Mr. Business Magazine